Raw Materials Definition Accounting And Direct Vs Indirect
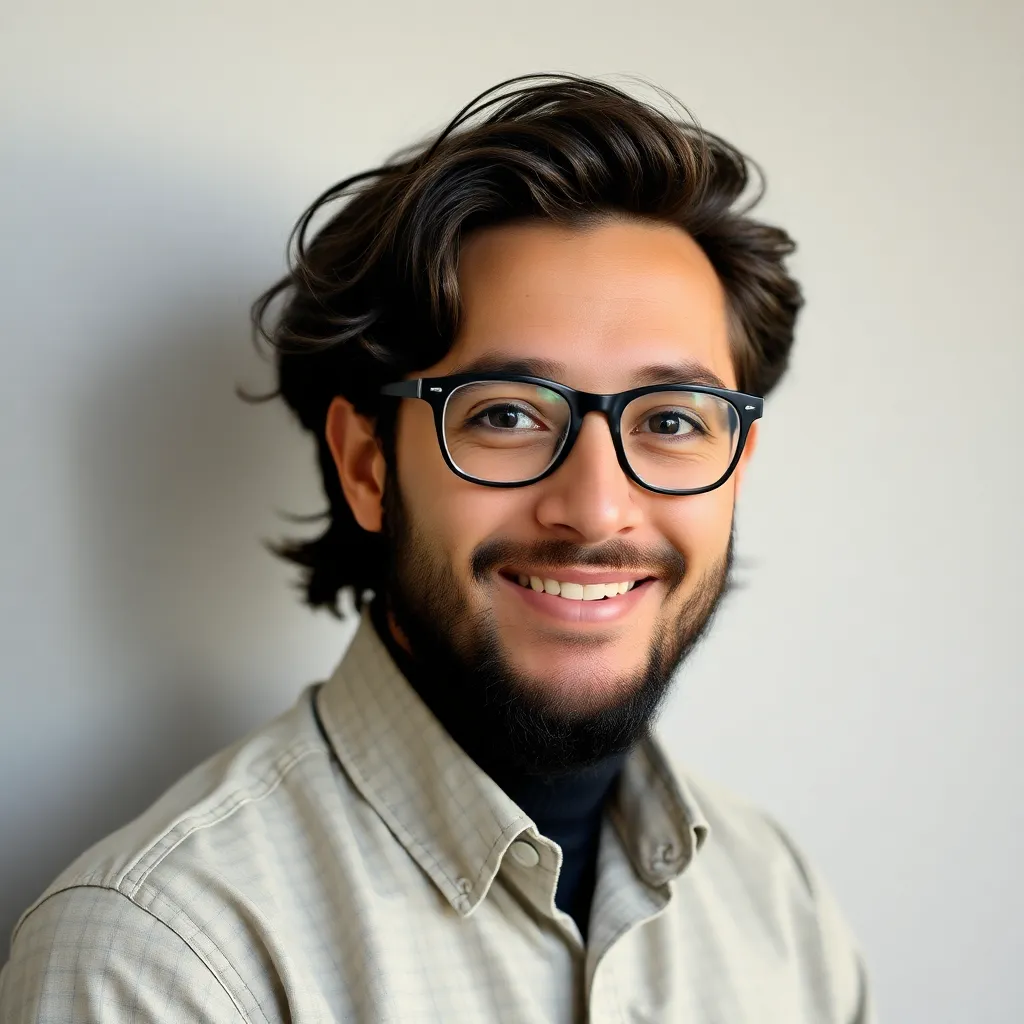
adminse
Mar 31, 2025 · 8 min read

Table of Contents
Unveiling the Essence of Raw Materials: Definition, Accounting, and Direct vs. Indirect Costs
What truly defines raw materials in the intricate world of accounting, and how do we differentiate between direct and indirect costs?
Understanding raw materials is fundamental to accurate financial reporting and effective cost management; a deep dive reveals crucial insights for informed decision-making.
Editor’s Note: This comprehensive analysis of raw materials in accounting, differentiating direct and indirect costs, has been published today.
Why Raw Materials Matter
Raw materials are the fundamental building blocks of any manufacturing or production process. Their accurate accounting is paramount for several key reasons:
- Costing Accuracy: Properly identifying and classifying raw materials is crucial for determining the cost of goods sold (COGS), which directly impacts profitability and pricing strategies. Inaccurate costing can lead to misinformed pricing decisions, impacting competitiveness and revenue.
- Inventory Management: Effective raw material management hinges on accurate accounting. Knowing the quantity and value of raw materials on hand allows businesses to optimize inventory levels, minimizing storage costs and preventing stockouts or overstocking.
- Financial Reporting: Accurate raw material accounting is essential for preparing reliable financial statements, complying with accounting standards (like GAAP or IFRS), and providing stakeholders with a clear picture of the company's financial health.
- Operational Efficiency: Tracking raw material usage and costs can highlight inefficiencies in the production process, enabling businesses to identify areas for improvement and cost reduction. This data-driven approach leads to leaner operations and enhanced profitability.
- Strategic Decision-Making: Understanding the cost and availability of raw materials is essential for strategic planning, such as negotiating better supplier contracts, exploring alternative materials, and making informed decisions about product pricing and market positioning.
Overview of the Article
This article delves into the core concepts surrounding raw materials in accounting. We will explore the precise definition of raw materials, examine the accounting treatment of these materials, and critically analyze the crucial distinction between direct and indirect raw material costs. Readers will gain a comprehensive understanding of how to accurately account for raw materials, enabling better cost control and informed business decisions.
Research and Effort Behind the Insights
This analysis draws upon extensive research, encompassing authoritative accounting texts, industry best practices, and real-world case studies. The information presented reflects a thorough understanding of accounting principles and their application to raw material management.
Key Takeaways
Key Concept | Description |
---|---|
Raw Material Definition | Materials directly used in the production process, transformed into finished goods. |
Direct Material Cost | Costs directly traceable to the production of finished goods (e.g., wood in furniture manufacturing). |
Indirect Material Cost | Costs indirectly related to production, difficult to trace to specific products (e.g., cleaning supplies). |
Raw Material Inventory Accounting | Methods like FIFO, LIFO, and weighted-average cost are used to value raw material inventory. |
Material Requisition Forms | Documents authorizing the release of raw materials from inventory for use in production. |
Cost of Goods Sold (COGS) | The direct costs associated with producing goods sold during a specific period. |
Smooth Transition to Core Discussion
Let's now embark on a detailed exploration of raw materials, beginning with their formal definition and progressing through the nuances of direct and indirect cost allocation.
Exploring the Key Aspects of Raw Materials Accounting
-
Definition and Classification: Raw materials are defined as any materials directly used in the manufacturing or production process and transformed into finished goods. They are distinct from work-in-progress (WIP) and finished goods. Classification involves categorizing materials based on their usage, such as primary materials, secondary materials, and consumables.
-
Accounting for Raw Materials: The accounting process involves recording the purchase, storage, and usage of raw materials. This necessitates maintaining accurate inventory records, using methods like perpetual or periodic inventory systems. Costing methods—FIFO (First-In, First-Out), LIFO (Last-In, First-Out), and weighted-average cost—determine the value of raw materials used in production.
-
Direct vs. Indirect Raw Materials: The core distinction lies in the traceability of costs. Direct materials are directly incorporated into the finished product and are easily traceable (e.g., fabric for clothing). Indirect materials are less directly traceable, contributing to the overall production process but not directly identifiable within a specific product (e.g., lubricants for machinery).
-
Material Requisition System: This formal process controls the release of raw materials from inventory. Material requisition forms authorize the transfer of materials to the production floor, ensuring accurate tracking and minimizing waste or unauthorized usage.
-
Cost of Goods Sold (COGS) Calculation: COGS represents the direct costs associated with the goods sold during a specific accounting period. Raw materials (both direct and a portion of indirect) are a major component of COGS, significantly impacting a company's profitability.
Closing Insights
Accurate raw material accounting is not merely a compliance exercise; it's a cornerstone of effective cost management and informed decision-making. By properly classifying materials, implementing robust inventory control systems, and accurately calculating COGS, businesses gain invaluable insights into their production processes, enabling them to optimize operations, enhance profitability, and maintain a competitive edge. The detailed tracking of direct vs. indirect costs allows for granular analysis, identifying areas for potential cost reduction and efficiency improvements. This granular level of understanding is essential for sustainable growth in any manufacturing or production-based enterprise.
Exploring the Connection Between Inventory Valuation Methods and Raw Materials
Different inventory valuation methods significantly impact the cost of goods sold and the value of ending inventory, affecting both profitability and the balance sheet. Let's examine how FIFO, LIFO, and weighted-average cost impact raw material accounting:
-
FIFO (First-In, First-Out): Assumes that the oldest raw materials are used first in the production process. During periods of inflation, FIFO results in a lower COGS and higher net income, as older, cheaper materials are expensed. Ending inventory reflects current market prices.
-
LIFO (Last-In, First-Out): Assumes that the newest raw materials are used first. In inflationary periods, LIFO results in a higher COGS and lower net income because the most recently purchased, higher-priced materials are expensed. Ending inventory reflects older, potentially outdated prices.
-
Weighted-Average Cost: Calculates the average cost of all raw materials available for sale during the period. This method smooths out price fluctuations and simplifies calculations, although it may not reflect the true cost of goods sold as accurately as FIFO or LIFO.
Further Analysis of Inventory Control Systems
Effective inventory control systems are critical for managing raw materials efficiently. Two primary systems are:
-
Perpetual Inventory System: Maintains continuous records of raw material inventory levels, updating balances with each purchase and usage. This provides real-time visibility into inventory levels, facilitating better planning and reducing stockouts.
-
Periodic Inventory System: Counts inventory at the end of a specific period (e.g., monthly or quarterly) to determine the quantity on hand. While simpler to implement, it lacks the real-time insights provided by a perpetual system.
FAQ Section
-
Q: What are some examples of indirect raw materials? A: Examples include lubricants, cleaning supplies, small tools, and packaging materials used in the overall production process but not directly incorporated into the finished product.
-
Q: How do I choose the right inventory valuation method? A: The choice depends on factors such as industry practices, tax regulations, and the company's specific circumstances. Consider the impact on financial statements and the accuracy of cost reporting.
-
Q: What is the importance of material requisition forms? A: They provide an audit trail for raw material usage, preventing unauthorized access and ensuring accurate cost tracking.
-
Q: How does raw material accounting affect profitability? A: Accurate raw material accounting directly impacts the calculation of COGS, which in turn influences the reported gross profit and net income.
-
Q: How can I improve my raw material inventory management? A: Implement robust inventory control systems, utilize forecasting techniques, and regularly review inventory levels to optimize stock and minimize waste.
-
Q: What are the implications of inaccurate raw material accounting? A: Inaccurate accounting can lead to misstated financial reports, incorrect pricing decisions, inefficient inventory management, and potentially legal ramifications.
Practical Tips for Effective Raw Material Management
-
Implement a robust inventory management system: Choose a system (perpetual or periodic) that aligns with your business needs and resources.
-
Use material requisition forms: Ensure all raw material withdrawals are properly documented and authorized.
-
Regularly review inventory levels: Identify slow-moving items and adjust ordering practices to minimize waste and storage costs.
-
Negotiate favorable supplier contracts: Secure competitive pricing and reliable supply chains.
-
Implement quality control measures: Ensure the quality of incoming raw materials meets specifications.
-
Utilize forecasting techniques: Predict future demand to optimize inventory levels and avoid stockouts.
-
Analyze raw material costs: Identify areas for potential cost reduction and explore alternative materials.
-
Regularly reconcile inventory records: Ensure physical inventory counts match recorded balances to prevent discrepancies.
Final Conclusion
Understanding raw materials and their accounting treatment is crucial for businesses of all sizes. The accurate classification of materials as direct or indirect, the careful selection of an inventory valuation method, and the implementation of a robust inventory control system are all key components of effective cost management. By mastering these concepts, businesses can enhance profitability, optimize operations, and make informed strategic decisions, ensuring sustained growth and success. The significance of accurate raw material accounting cannot be overstated; it underpins financial reliability, facilitates effective decision-making, and forms the bedrock of a healthy and thriving enterprise.
Latest Posts
Related Post
Thank you for visiting our website which covers about Raw Materials Definition Accounting And Direct Vs Indirect . We hope the information provided has been useful to you. Feel free to contact us if you have any questions or need further assistance. See you next time and don't miss to bookmark.