Quality Management Definition Plus Example
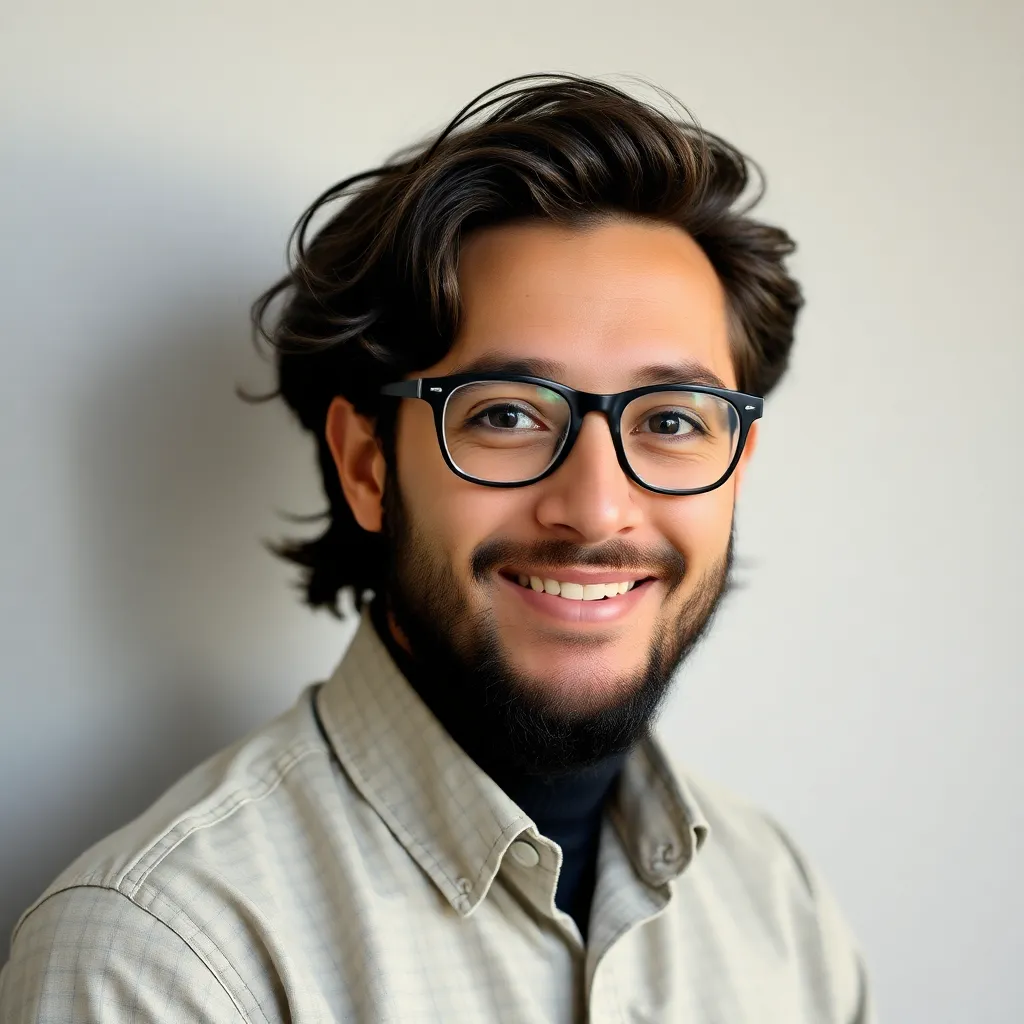
adminse
Mar 31, 2025 · 9 min read

Table of Contents
Defining and Implementing Quality Management: A Comprehensive Guide with Real-World Examples
What sets truly exceptional organizations apart from the rest?
The unwavering commitment to quality management—a systematic approach that transforms challenges into opportunities and fuels sustained success.
Editor’s Note: This comprehensive guide to Quality Management definitions and examples has been published today, offering the latest insights and practical applications for businesses of all sizes.
Why Quality Management Matters
In today's fiercely competitive global marketplace, delivering consistent quality is no longer a luxury—it's a necessity for survival. Quality management (QM) transcends mere defect reduction; it's a holistic philosophy that permeates every aspect of an organization, impacting product development, customer satisfaction, operational efficiency, and ultimately, the bottom line. It fosters a culture of continuous improvement, driving innovation and adaptability in the face of evolving market demands. From manufacturing giants to small startups, organizations that prioritize QM gain a significant competitive edge by improving brand reputation, reducing waste, enhancing productivity, and fostering stronger customer loyalty. This translates to increased profitability, enhanced employee morale, and a sustainable growth trajectory.
Overview of This Article
This article delves into the core principles of quality management, exploring its multifaceted nature and practical applications across diverse industries. Readers will gain a nuanced understanding of QM frameworks, learn how to implement effective QM systems, and discover how to leverage quality management principles to achieve sustainable competitive advantage. We will examine real-world examples to illustrate the power and versatility of quality management practices.
Research and Effort Behind the Insights
The insights presented in this article are the result of extensive research, drawing on established quality management standards (ISO 9001, Six Sigma, Lean), case studies from leading organizations, and expert opinions from renowned quality management professionals. A rigorous, data-driven approach ensures the accuracy and relevance of the information provided.
Key Takeaways
Key Aspect of Quality Management | Description | Example |
---|---|---|
Definition & Principles | A structured approach to ensure consistent product/service quality. | Meeting customer expectations and exceeding them consistently. |
QM Frameworks (ISO 9001) | Internationally recognized standards for QM systems. | Implementing documented procedures, regular audits, and continuous improvement cycles. |
Tools & Techniques (Six Sigma) | Statistical methods to identify and reduce variation. | Using DMAIC (Define, Measure, Analyze, Improve, Control) to optimize processes and reduce defects. |
Continuous Improvement (Kaizen) | Small, incremental improvements over time. | Regularly identifying and addressing areas for improvement in all operational aspects. |
Customer Focus | Prioritizing customer needs and expectations. | Gathering customer feedback through surveys, focus groups, and direct interaction. |
Employee Engagement | Empowering employees to contribute to QM efforts. | Training staff on quality procedures, encouraging feedback and suggestions, and fostering teamwork. |
Let’s dive deeper into the key aspects of quality management, starting with its foundational principles and real-world applications.
1. Defining Quality Management
Quality management encompasses all activities involved in establishing and maintaining a consistently high quality of goods or services. This involves setting clear quality standards, implementing processes to meet those standards, monitoring performance against those standards, and continually improving the quality management system itself. It's a proactive and preventative approach, aiming to eliminate defects and minimize errors before they occur, rather than simply reacting to problems after they arise. The core objective is to meet and exceed customer expectations while optimizing efficiency and profitability.
2. Key QM Frameworks and Standards
Several widely adopted frameworks provide structured guidance for implementing effective quality management systems. The most prominent is ISO 9001, an internationally recognized standard that outlines requirements for a robust QM system. Certification to ISO 9001 demonstrates an organization’s commitment to quality and provides a competitive advantage in the marketplace. Other frameworks include Six Sigma, which uses statistical methods to minimize process variation and improve quality, and Lean manufacturing, which focuses on eliminating waste and optimizing efficiency.
Example: ISO 9001 Implementation in a Manufacturing Company
A manufacturing company seeking ISO 9001 certification would need to implement a quality management system that encompasses:
- Quality Policy: Defining the organization's commitment to quality and objectives.
- Documentation: Establishing documented procedures for all key processes.
- Resource Management: Ensuring adequate resources (equipment, personnel, training) are available.
- Product Realization: Controlling all aspects of product design, production, and delivery.
- Measurement, Analysis, and Improvement: Regularly monitoring performance, analyzing results, and implementing corrective actions.
- Management Review: Regularly reviewing the effectiveness of the QM system and making improvements as needed.
3. Tools and Techniques for Quality Management
A range of tools and techniques support the implementation and continuous improvement of quality management systems. These include:
- Statistical Process Control (SPC): Using statistical methods to monitor and control processes.
- Control Charts: Visual tools for tracking process variation over time.
- Pareto Charts: Identifying the most significant causes of defects.
- Fishbone Diagrams (Ishikawa diagrams): Analyzing the potential causes of a problem.
- Root Cause Analysis (RCA): Investigating the underlying causes of problems.
- 5S Methodology: Organizing and maintaining a clean and efficient workplace (Sort, Set in Order, Shine, Standardize, Sustain).
Example: Six Sigma in a Customer Service Department
A customer service department might use the DMAIC (Define, Measure, Analyze, Improve, Control) cycle of Six Sigma to reduce customer complaints. This would involve:
- Define: Clearly defining the problem (e.g., high call wait times).
- Measure: Collecting data on call wait times, customer satisfaction scores, and other relevant metrics.
- Analyze: Identifying the root causes of long wait times (e.g., insufficient staffing, inefficient processes).
- Improve: Implementing solutions to address the root causes (e.g., hiring additional staff, streamlining processes).
- Control: Monitoring the improvements to ensure they are sustained over time.
4. Continuous Improvement (Kaizen)
Continuous improvement is a fundamental principle of quality management. It emphasizes the ongoing effort to identify and eliminate inefficiencies, reduce waste, and improve processes. Kaizen, a Japanese term meaning "change for the better," embodies this philosophy, focusing on small, incremental improvements rather than large-scale changes. This approach encourages employee participation, fostering a culture of continuous learning and innovation.
Example: Kaizen in a Manufacturing Plant
A manufacturing plant might implement Kaizen by:
- Regularly reviewing production processes: Identifying bottlenecks and areas for improvement.
- Encouraging employee suggestions: Implementing employee-driven improvements.
- Implementing small, incremental changes: Making frequent, minor adjustments to optimize processes.
- Tracking and measuring results: Monitoring the impact of implemented changes.
5. The Crucial Role of Customer Focus
Customer focus is paramount in quality management. Understanding and meeting customer needs and expectations is essential for achieving customer satisfaction and loyalty. This involves actively seeking customer feedback, analyzing customer data, and using this information to improve products, services, and processes.
Example: Customer Feedback in a Retail Setting
A retail store might collect customer feedback through:
- Customer surveys: Gathering feedback on product quality, service, and overall shopping experience.
- Focus groups: Conducting in-depth discussions with customers to gain insights into their needs and preferences.
- Social media monitoring: Tracking customer opinions and feedback on social media platforms.
6. Employee Engagement in Quality Management
Effective quality management requires the active participation and engagement of all employees. Empowering employees to contribute to quality improvement efforts, providing them with the necessary training and resources, and creating a culture of collaboration are crucial.
Example: Employee Involvement in a Food Processing Facility
A food processing facility might engage employees in quality management by:
- Providing training on quality control procedures: Ensuring employees understand quality standards and how to contribute to their achievement.
- Establishing suggestion boxes and reward programs: Encouraging employees to share their ideas for improvement.
- Creating cross-functional teams: Involving employees from different departments in quality improvement projects.
7. Exploring the Connection Between Risk Management and Quality Management
Risk management and quality management are deeply intertwined. Effective quality management requires a proactive approach to identifying and mitigating potential risks that could affect product or service quality. This involves conducting risk assessments, developing risk mitigation strategies, and monitoring risks throughout the product lifecycle.
Further Analysis of Risk Management in Quality Management
Risk Type | Potential Impact on Quality | Mitigation Strategy |
---|---|---|
Supplier Risks: Poor quality materials from suppliers. | Defective products, production delays. | Implement rigorous supplier selection and evaluation processes; establish clear quality requirements for suppliers. |
Process Risks: Inefficient or poorly controlled processes. | High defect rates, inconsistent product quality. | Improve process design, implement SPC, provide adequate employee training. |
Environmental Risks: Changes in environmental conditions. | Damage to products, production interruptions. | Implement robust environmental monitoring and control measures. |
Human Error: Mistakes by employees. | Defective products, safety hazards. | Provide adequate training, implement robust quality control checks, foster a culture of safety. |
8. Frequently Asked Questions (FAQ)
Q1: What is the difference between quality control and quality management? Quality control focuses on inspecting finished products to identify defects, while quality management is a broader, proactive approach that encompasses all aspects of ensuring quality throughout the entire product lifecycle.
Q2: How can small businesses implement quality management? Small businesses can implement QM by focusing on key processes, using simple tools and techniques, and involving all employees in quality improvement efforts.
Q3: What are the benefits of ISO 9001 certification? ISO 9001 certification demonstrates a commitment to quality, enhances credibility, improves efficiency, and can open doors to new business opportunities.
Q4: How can quality management improve customer satisfaction? By consistently meeting and exceeding customer expectations, reducing defects, and providing excellent customer service.
Q5: What is the role of leadership in quality management? Leaders must establish a strong quality culture, provide resources, support employee engagement, and champion continuous improvement efforts.
Q6: How can technology help with quality management? Technology such as data analytics, automation, and quality management software can streamline processes, improve data collection and analysis, and enhance efficiency.
9. Practical Tips for Implementing Quality Management
- Define clear quality standards: Establish specific, measurable, achievable, relevant, and time-bound (SMART) goals.
- Document all key processes: Create detailed procedures to ensure consistency.
- Train employees on quality procedures: Provide adequate training and resources.
- Implement regular quality audits: Monitor performance and identify areas for improvement.
- Collect and analyze customer feedback: Use customer feedback to improve products and services.
- Encourage employee involvement: Empower employees to contribute to quality improvement.
- Implement continuous improvement initiatives: Continuously seek ways to improve processes and reduce waste.
- Use appropriate quality management tools and techniques: Leverage tools such as SPC, control charts, and root cause analysis.
Final Conclusion
Quality management is not merely a set of procedures; it's a transformative philosophy that empowers organizations to achieve sustained success. By embracing a culture of continuous improvement, focusing on customer needs, and engaging employees at all levels, organizations can unlock significant benefits, including enhanced profitability, improved brand reputation, and strengthened customer loyalty. The examples and practical tips outlined in this article provide a roadmap for successfully implementing quality management principles and realizing their transformative potential. The journey toward achieving excellence in quality management is an ongoing process of learning, adapting, and striving for constant improvement. The rewards, however, are immeasurable, positioning organizations for lasting success in an increasingly competitive global market.
Latest Posts
Related Post
Thank you for visiting our website which covers about Quality Management Definition Plus Example . We hope the information provided has been useful to you. Feel free to contact us if you have any questions or need further assistance. See you next time and don't miss to bookmark.